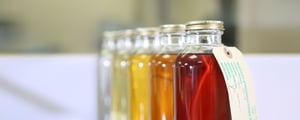
TRANSTEST OIL SAMPLE TESTING
As part of the ‘one stop shop’ of insulating oil related services and products, EOS has partnered with one of the UK’s leading insulating oil testing and analytical services to provide expert fluid quality testing.
Drawing on our distinct capabilities to bring a unique oil analysis service known as TransTest, EOS control the service from issue of bottles, sample training and guidance, collection of samples and carriage to our partner laboratory where turnaround time is strictly monitored and guaranteed to be within 7 working days of receipt in the laboratory.
The process
The EOS TransTest Oil Sample Testing service was developed at a time when the UK industry was first privatised and complemented the EOS “one stop shop” for insulating oil requirements. The TransTest was the first service able to offer:
-
A guaranteed 7 working day turnaround
-
Supply of clean new sample bottles
-
A return courier to the lab
The service was originally carried out in-house by Carless and Castrol, but following the formation of EOS in 1999 the decision was made to form a strategic partnership with a specialised insulating oil laboratory. EOS therefore works in partnership with the UK’s leading electrical oil test house TJh2b, and together we are able to offer a unique service combining the skills and expertise of the EOS Engineering team with the experience and breadth of knowledge of TJh2bs Chemists.
Detailed analysis of a transformer oil sample, like a blood test, can reveal much about the state of health of the oil and the transformer. To keep your transformer oil (and hence your transformer) in a healthy state, follow these simple guidelines:
Keep cool – every 6°C reduction in transformer operating temperature doubles the life of the transformer, so run pumps or fans if fitted and ensure your transformer is adequately ventilated.
Sample regularly – taking a sample that is “representative” of the body of the oil is the first and most important step in the testing and analysis process – guidelines can be found here.
Customise your tests – depending on the criticality of your transformer, EOS engineers can advise you on what tests you need to carry out and why.
Act early – where your transformer is critical to the operation of your site, early intervention to restore oil quality to “as new” will ensure damage to critical paper insulation is limited. The use of a Mobile Processing Unit or Mobile Regeneration Unit at an early stage in the oil degradation process is recommended.
To find out more about the TransTest Oil Sample Testing service, please contact a member of the customer service team. We can offer help and guidance on subjects such as how to to take reliable samples, and helping to interpret test results.
Oil testing is almost like having a blood sample taken. A properly taken sample can tell the asset owner everything, from the general health of the oil at one extreme, to whether the transformer is about to fail at the other.
A well thought out sampling and testing regime can feed into a more strategic transformer asset management plan. By customising the testing to the importance of the transformer, a focused and cost effective plan can be developed.
EOS engineers have over 50 years field experience and can offer best advice from sampling technique to what tests are required – this is all part of the complete solution that EOS offers.
Because EOS has teamed up with TJh2b, the UK’s leading specialist insulating oil test house, we are able to offer more than just oil analysis.
The complete range of tests ranges from simple oil tests to sophisticated analysis of the oil to determine paper strength. Trend analysis of dissolved combustible gasses can also help predict transformer failure before it happens.
In reality, the tests you require will vary depending on a large number of engineering and commercial factors – Our expert team of EOS engineers can discuss this with you and help identify the most appropriate method.
For more information about which tests you might need, please get in touch with James Clifford, who will be happy to talk you through the process. Call James on 0845 602 1003 or email: cliffordJ@electricaloilservices.com
Why should I use a glass sampling thief?
There are three reasons for favouring glass for sampling thieves.
- It is resistant to scratching, which can harbour contamination.
- It is relatively easy to keep clean.
- It is quite evident when it is not clean.
How should I take a sample of oil from a Drum?
The purpose of sampling is to produce an accurate representation of the body of the oil, ensuring any contaminants present are found, while excluding those from external sources. It should be remembered that all contact with air, sampling equipment etc. could have an influence on the sample. Ideally, all external influences, such as airborne contamination, rain, dust etc. should be totally excluded. In some cases, where sampling under poor conditions is necessary, this may mean the erection of a small tent or makeshift cover. A 500ml sample will be sufficient to carry out all routine, PCB and DGA tests.
Allow the oil in the drum to acclimatise by achieving equilibrium with the ambient temperature. Clean the area around the bung. Remove the tab-seal and the bung using a drum key. Inspect the bung seal for signs of damage or contamination. Remove your glass sampling thief from its protective case and inspect and wipe the outside of it. Insert the thief into the oil about half way, place a finger or thumb over the top end and withdraw. The thief is now half full of oil. This is used to rinse the inside of the thief by rocking it in a “see-saw” motion while rolling it to ensure total rinsing of the internal surface. This should be done over a large drip-tray. Repeat and examine. Using the same technique as above, withdraw half a thief of oil and place it in the sample bottle. Rest the thief in the oil drum where it will be safe and clean. The sample bottle is then capped and rinsed by vigorously shaking it. Continue shaking while discarding oil to prevent any contaminants adhering to the side of the bottle. Repeat and examine.
To take a sample from the bottom of the drum, which is where any contaminants, if present, are most likely to be found, insert the thief into the drum ensuring that the finger or thumb covering the top hole is not removed until the thief reaches the bottom of the drum. Then uncover the hole allowing oil from the bottom of the drum to enter the thief. While this is happening, the thief should be moved across the bottom of the drum and around the bottom seam. When the oil level in the thief is the same as that in the drum, uncap the sample bottle and cover the top hole of the thief and withdraw it from the drum lifting it vertically. Hold the bottle over a bucket or drip tray, and, without placing the end of the thief in the top of the bottle, uncover the top hole and aim the oil into the sample bottle such that it flows down it’s side. Repeat until the bottle is full and overflowing. The overflowing will help to release any air bubbles from the bottle. Pour the surplus oil from the bottle over the cap to rinse. Leave a 0.5-1cm air gap and finger tighten the cap. Be careful not to over-tighten. Replace bung to drum. Gently invert the sample bottle and inspect for visible solid contamination and/or free water. If contamination is found, the sample should be discarded and the above procedure repeated to ensure that the first was representative. Complete the sample data sheet or label in full.
How should I take a sample of oil from a Switch Tank?
Although it is normal practice to remove oil from switch gear for maintenance and replace with oil of a known and certified quality standard, samples, either “as found” or “as left” are often taken for diagnostic or statistical purposes.
The purpose of sampling is to produce an accurate representation of the body of the oil, ensuring any contaminants present are found, while excluding those from external sources. It should be remembered that all contact with air, sampling equipment etc. could have an influence on the sample. Ideally, all external influences, such as airborne contamination, rain, dust etc. should be totally excluded. In some cases, where sampling under poor conditions is necessary, this may mean the erection of a small tent or makeshift cover. A 500ml sample will be sufficient to carry out all routine, PCB and DGA tests.
Clean the switch lid, paying particular attention to the external rim of the gasket seat, a favourite home of insects. Remove the switch lid and carry out a visual inspection. Using a torch if necessary, check as much of the base of the tank as possible, especially in corners and directly beneath any access covers, sight glasses or operating mechanism bushes. Record the nature and location of any contamination found. Remove your glass sampling thief from its protective case and inspect and wipe the outside of it. Insert the thief into the oil short of the tank bottom, place a finger or thumb over the top end and withdraw. The thief is now about half full of oil.
This is used to rinse the inside of the thief by rocking it in a “see-saw” motion while rolling it to ensure total rinsing of the internal surface. This should be done over a large drip-tray. Repeat and examine. Using the same technique as above, withdraw half a thief of oil and place it in the sample bottle. Rest the thief in the switch tank where it will be safe and clean. The sample bottle is then capped and rinsed by vigorously shaking it. Continue shaking while discarding oil to prevent any contaminants adhering to the side of the bottle. Repeat and examine.
To take a sample from the bottom of the switch, which is where any contaminants, if present, are most likely to be found, insert the thief into the switch ensuring that the finger or thumb covering the top hole is not removed until the thief reaches the bottom of the tank. Uncover the hole allowing oil from the bottom to enter the thief.
While this is happening, the thief should carefully be moved across the bottom of the tank as much as possible. When the oil level in the thief is the same as that in the switch, uncap the sample bottle and cover the top hole of the thief and withdraw it from the switch lifting it vertically. Hold the bottle over a bucket or drip tray, and, without placing the end of the thief in the top of the bottle, uncover the top hole and aim the oil into the sample bottle such that it flows down it’s side. Repeat, taking successive dips from different parts of the switch, until the bottle is full and overflowing. The overflowing will help to release any air bubbles from the bottle.
Pour the surplus oil from the bottle over the cap to rinse. Leave a 0.5-1cm air gap and finger tighten the cap. Be careful not to over-tighten. Gently invert the sample bottle and inspect for visible solid contamination and/or free water. If contamination is found, the sample should be discarded and the above procedure repeated to ensure that the first was representative. Complete the sample data sheet or label in full.
How should I take a sample of oil from a transformer?
The purpose of sampling is to produce an accurate representation of the body of the oil, ensuring any contaminants present are found, while excluding those from external sources. It should be remembered that all contact with air, sampling equipment etc. could have an influence on the sample. Ideally, all external influences, such as airborne contamination, rain, dust etc. should be totally excluded. In some cases, where sampling under poor conditions is necessary, this may mean the erection of a small tent or makeshift cover. A 500ml sample will be sufficient to carry out all routine, PCB and DGA tests.
If there is not a dedicated sample point provided, fit a sampling adapter to a drain valve or filter valve. Ensure that the exterior of the valve and adapter is clean before fitting. Open the valve and establish a controllable & directional flow into a bucket. Use a plastic hose kept especially for the purpose. Clean the interior of the valve, sample adapter and hose by flushing with oil, allow 2-3 litres to flow to ‘waste’ – do not adjust the flow rate from now on. Record the oil temperature as the flushing oil runs into the bucket. Do not put the thermometer into the sample bottle. Rinse the sample bottle 2 or 3 times by half filling it and vigorously shaking it.
Continue shaking while discarding oil to prevent any contaminants adhering to the side of the bottle. Repeat and inspect for cleanliness. Fill the bottle gently by directing the flow down the side to reduce aeration until the bottle is full and overflowing.
The overflowing will help to release any air bubbles from the bottle. Run some oil over the cap to rinse it. Leave a 0.5-1cm air gap and finger tighten the cap. Be careful not to over-tighten. Close the sample valve. Gently invert the sample bottle and inspect for visible solid contamination and/or free water. If contamination is found, the sample should be discarded and the above procedure repeated to ensure that the first was representative. Complete the sample data sheet or label in full.
My transformers are only small but they feed critical services, what oil tests can I do to monitor their condition?
In many instances, the value of an item of oil-filled plant will not be related to its capital cost, but to the importance of the load it supplies. Hence even relatively small, low rating and low cost plant can justify the performance of sophisticated monitoring techniques such as dissolved gas analysis (DGA).
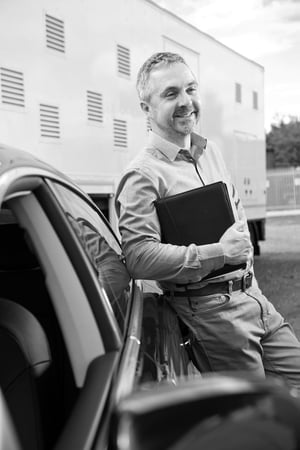
Speak to the
experts
experts
Case Studies
Specialised oil testing
The customer was a major steel manufacturer in the North East of England, who made initial contact with EOS as…
TransTest User Information
Customer Service Administrator
James Clifford
Tel: 0845 6021003
Email: jclifford@h-c-s-group.com
Unused Inhibited Insulating Oil
Reclaimed Uninhibited Insulating Oil
It’s our extensive experience in the (in-situ) treatment, storage and supply of insulating oil that gives our customers peace of mind when it comes to the quality and standard of our services.
Not only do we supply unused and regenerated insulating oil, but we also provide a range of robust complimentary products.
Our people are passionate about what they do, giving honest, pure, expert advice on a subject they know inside and our.