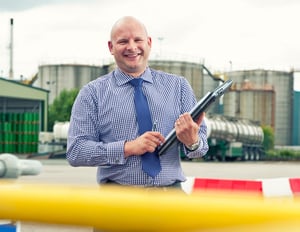
Martin is one of our dedicated Field Service Managers, whose combined technical and operational knowledge is a part of what makes EOS the trusted innovative supplier of choice when it comes to electrical insulating oil.
Martin started his career in 1995, working as an Industrial Placement Student GEC Alsthom in the high-voltage switchgear department whilst studying Electrical Engineering.
The next 10 years saw Martin work in a number of different roles within the industry; from compiling orders for high voltage switchgear and working as a Contracts Engineer, to moving into transformer distribution and managing the transportation of transformers all over the world. Before joining the team at EOS, Martin was a project leader involved in the service and maintenance of transformer installations and their transportation.
With this wealth of practical knowledge and experience, Martin joined the team at EOS in 2014, where he took up the position of Area Manager and later on as Field Service Manager.
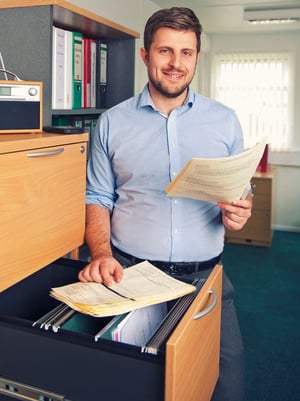
Tom leads an office team that is the first point of contact for many of our customer interactions and responsible for driving continuous improvement in the way we provide good service to our customers.
Tom joined EOS in 2010 as part of the Customer Services team, before being appointed Customer Services Manager the following year. In 2014, Tom was given account management responsibilities for our high voltage contractors, which means he now splits his time between these dual roles. Tom is responsible for maintaining and developing working relationships with many of our customers, but specifically our contractor customers working on high voltage networks.
Tom works closely with our clients and during his time at EOS has gained excellent knowledge of their specific needs, from details about individual delivery locations to personnel requirements. It is this level of customer service and attention to detail that has allowed EOS to develop strong long-term relationships with many of our clients. Tom is proud to lead a team that provides a complete, quality service, from the contact customers have with office-based staff, all the way through to their experience with the EOS technical teams on-site.
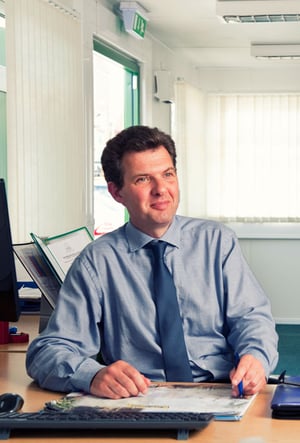
Mike is responsible for the EOS operations at our Stanlow site. Additionally, he manages our Base Oil product line.
Mike has been with the team since April 2000, having spent his entire career in the oil and chemical industry with companies such as Dexter Speciality Chemicals and Arizona Chemicals. He graduated university in 1988 with a degree in Accounting and Finance, before later qualifying as a Chartered Management Accountant in 1990.
When EOS was formed in 1999, it was a joint venture between Castrol UK and Carless. Mike was the first employee of the joint venture company as a result of both shareholders wanting to recruit a financial controller who was impartial and had not previously worked for either of the partners.
Mike now has a wide ranging role, which includes responsibility for accounting and finance, customer services and administration department, freight/transport, sales of base and process oils, raw material purchasing and stock control.
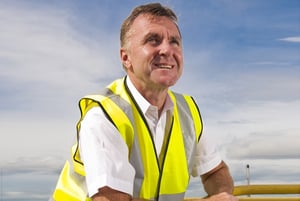
Tony is responsible for overseeing the treatment of hazardous waste, engineering and maintenance functions, managing quality, health, safety & environmental arrangements and liaising with the competent authorities.
Tony joined the team in 2001, having previously worked for three large oil and chemical manufacturers in quality and production roles.
As Plant & SHEQ Manager, Tony is responsible for the treatment of hazardous waste to create a product meeting industry specifications, overseeing the related process, engineering and maintenance functions, managing quality, health, safety & environmental arrangements and liaising with the competent authorities.
As well as his experience in the industry, Tony is supported by the knowledge that he has gained through a number of qualifications including:
- Bsc (Hons) Chemistry at University of Manchester; MRSC (Royal Society of Chemistry); Higher National Certificate in Science
- NEBOSH Diploma in Occupational Health & Safety; Graduate Member of IOSH
- Waste Management COTC (Certificate of Technical Competence) Issued through WAMITAB; NVQ level 4 in Hazardous Waste Management Operations
- Certificate in Environmental Management; Associate Member of IEMA
It’s our extensive experience in the (in-situ) treatment, storage and supply of insulating oil that gives our customers peace of mind when it comes to the quality and standard of our services.
Not only do we supply unused and regenerated insulating oil, but we also provide a range of robust complimentary products.
Our people are passionate about what they do, giving honest, pure, expert advice on a subject they know inside and our.