The exact time to replace the oil in transformers depends on factors such as the type of transformer, the operating conditions and the manufacturer's recommendations. However, as a general guideline, insulating oil samples should be taken and tested at least every five years to assess the condition of the insulating oil. Only this assessment determines the need for a change and helps to save costs. Learn more about the importance and benefits of transformer oil analysis in this blog, and explore additional linked resources.
Regular monitoring of transformer oil is essential to ensure optimal performance. Taking proactive steps can help avoid changing the oil earlier than necessary.
Saving costs and more: This is the reason why transformer oil analyses are useful
1. Identify vulnerabilities and increase service life
Transformer oil analyses assess the condition of transformers and facilitate the early implementation of measures to prevent downtimes and consequential damage. This is because the degradation and decomposition products dissolved in the insulating oil provide important information about possible deficiencies in the transformers. These are the two tests that help to determine the quality of the oil:
-
Dielectric-chemical tests that relate to the insulating oil quality
-
Gas and liquid chromatographic tests that relate to specified values
2. Increase informative value in insurance claims and other obligations
One of the most frequent causes of malfunctions in transformers is the insulating oil, and inspections of transformers often have insurance-relevant significance. Because one thing is clear: there are liability risks in the event of compliance violations. Due to the obligation to provide evidence, you should therefore not only ensure that your transformer oil is checked regularly, but also that the results of the analysis are properly documented and managed.
3. Avoiding supply bottlenecks of grid components
In order to avoid supply bottlenecks of network components with transformers, it is important on the one hand that companies manage their inventory in a timely manner. In addition, forward-looking insulating oil analyses help to avoid bottlenecks. After all, transformers now have to be available longer than in the past, and operating costs should be reduced to a maximum, especially in the energy sector.
4. Avoiding the risk of failure and increasing operational safety
Cost-intensive production downtimes can be avoided if the quality of the insulating medium is maintained at a high level. Damage to the insulation materials due to e.g. contamination, inadequate ambient conditions or higher loads is detected in good time through appropriate regular analyses.
When is it necessary to change the transformer oil?
An oil change should always be based on sound analysis results. Factors such as a high acid number, increased moisture content or reduced breakdown voltage are clear indicators that an oil replacement is required. Regular inspections of transformer oil help reduce the risk of unexpected failures and extend the lifetime of your equipment.
Checklist: Signs that an oil change may be necessary
- Noticeable discolouration of the insulating oil
- High acid content (analysis values outside the norm)
- Increased water content
- Declining dielectric strength
- Gas formation detected in the oil
- Prolonged downtime of the transformer
What are the costs involved in replacing insulating oil – and how can the oil in transformers be changed sustainably?
The costs depend on several factors:
- Quantity and type of oil
- Scope of preparatory work (e.g. cleaning, dismantling)
- Disposal of the used oil
- Labour time and travel costs
Compared to an unplanned failure or costly repairs, the preventive replacement of transformer oil represents a financially sound investment.
Sustainable asset management for transformers is increasingly recognised as a key value driver. This is due in part to current supply chain challenges, but also to increasing legal requirements regarding environmental protection.
Once test results show that the properties of the transformer oil have significantly deteriorated or that contamination has been detected, the question arises as to how best to carry out the oil change in the transformer.
To restore the required quality of the transformer oil, there are various options. These include drying, filtering and degassing in an oil treatment unit, on-site regeneration, or an oil replacement.
Read in this article which options are recommended as sustainable - such as the transformer oil regeneration:
Or use this article with useful practical tips as the next step:
Reduce your company's carbon footprint with the right transformer oil maintenance
In view of increasing environmental awareness and EU-wide requirements, there are certainly also good solutions for your transformer oil management. Especially recycled or regenerated insulating oils can score points here.
Find out more on how to easily save CO₂ and valuable resources:
-
High-quality, sustainable & like new: regenerated transformer oils
-
How cost-efficient & sustainable is the recycling of transformer oil?
Conclusion: Consistently check the oil in your transformers
The scheduled analysis of transformer oil, as well as the timely replacement of the insulating oil, are crucial to ensure the operational safety and economic efficiency of your equipment. Make these measures a fixed part of your transformer maintenance routine to save costs and resources in the long term.
Our tip: Consistently analyse the oil in transformers to determine the optimal time for an oil change! Because insulating oil analyses are an important part of transformer monitoring. Regular transformer oil samples lead to more safety in the power supply as well as to better planning of your asset management budget. This minimises short-term negative surprises.
In general, we answer the question: When to replace the oil in transformers? with two counter-questions:
Do you have any questions? We will be happy to answer them.
This blog was first published on June 20, 2023 and updated on April 22, 2025.
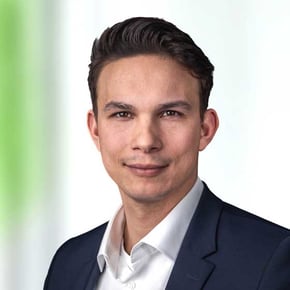