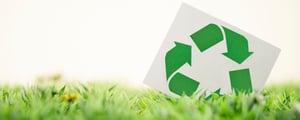
INSULATING OIL REGENERATION
For long-lasting deep cleansing
PREMIUM TREATMENT OF THE
ENTIRE INSULATING OIL SYSTEM OF A TRANSFORMER
Preventing failures, loss of performance and damage to transformers: With around 70 years of experience, Electrical Oil Services (EOS®) is one of the leading providers for the sustainable regeneration of transformer oils.
If you wish, EOS® regenerates the insulating liquid directly at the location of the transformer in a mobile process. During this insulating oil regeneration, not only the insulating oil but the entire insulating system of the transformer is treated. Whether under load, out of service or tank-to-tank during transformer maintenance.
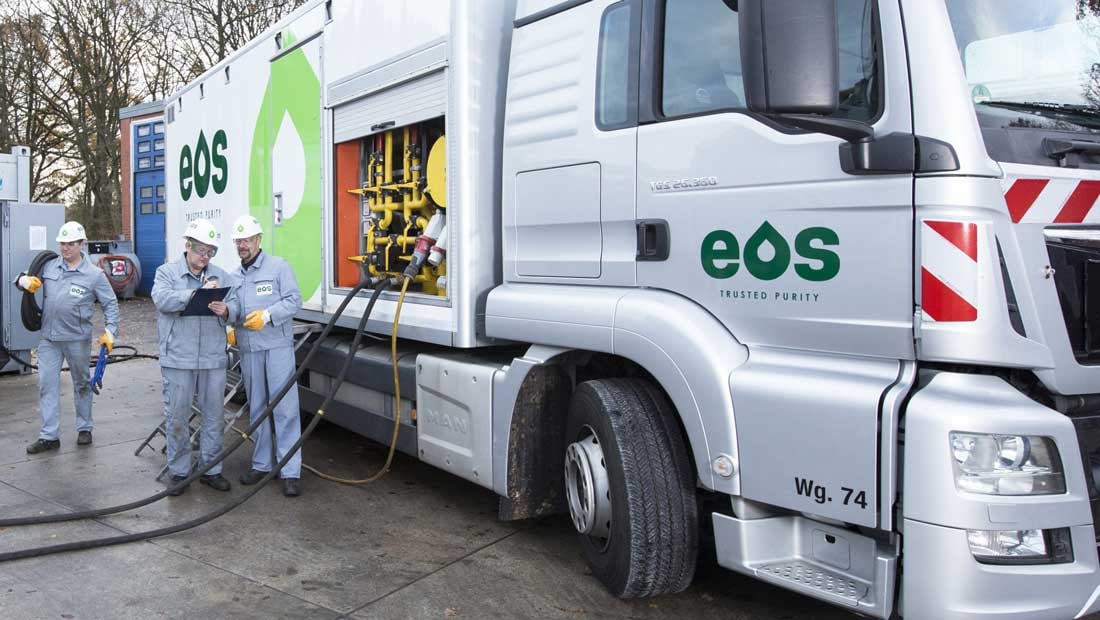
AS ENERGY SUPPLIER,
YOU BENEFIT FROM THE INSULATING OIL REGENERATION:
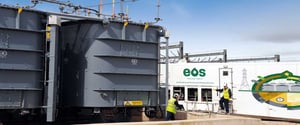
The service life of transformers is significantly increased by deep cleaning. This is because in addition to the transformer oil, the entire insulation system, including filter paper, is treated.
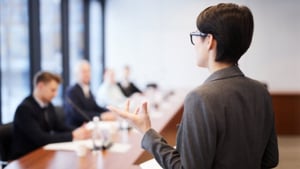
Our experts accompany the regeneration process from the initial investigation to the final report. And beyond that for all upcoming follow-up measures - if you wish.
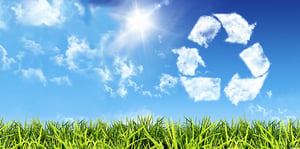
You do not have to buy new transformer oil. This saves significant costs, preserves precious natural resources and contributes to the circular economy.
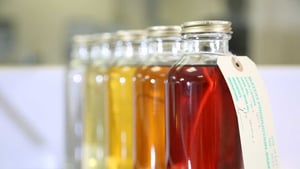
Deep cleaning captures far more insulating oil than an oil change - up to 97 percent of the oil content of a transformer.
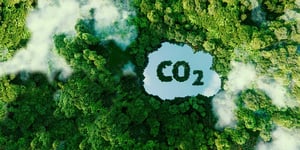
You significantly reduce your CO₂ emissions compared to virgin oil refilling.
Talk to our experts.
Schedule your individual consultation now!
FULL SUPPORT DURING THE OIL REGENERATION PROCESS
First of all, target vs. actual comparisons of the transformer oil and equipment condition are determined, as well as a detailed site analysis being carried out and documented.
Based on the preliminary investigations, EOS® defines in writing the ideal process for the respective customer and site.
Once the planning has been completed, the transformer oil is regenerated in five steps:
- Step 1: Initial treatment in the mobile regeneration unit (MRU).
- Step 2: Introduction of the transformer oil into the process columns.
- Step 3: Repetition of the regeneration process.
- Step 4: Reactivation of the process columns
- Step 5: Inhibition of the transformer oil with concentrate
More in-depth information in our EOS® blog Minimising effort and costs: Regenerating transformer oil on the move. Here you will also find a guide with the initial questions we will ask you if you are considering an insulating oil regeneration. |
OUR MATCHING PRODUCTS
EOS® Premium insulating oil
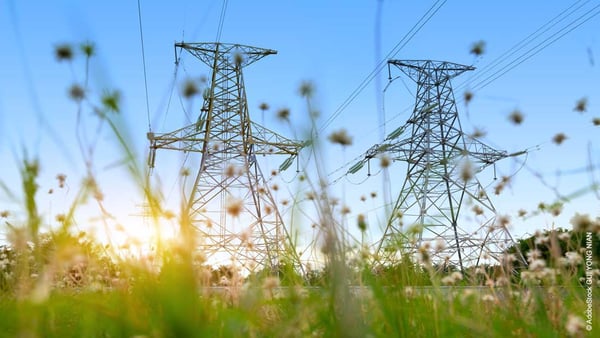
Read more about our as-new recycled insulating oil in this blog:
→ For transformers: Recycled EOS® Premium insulating oil proves its worth
→ EOS® Premium - Recycled Insulating Oil
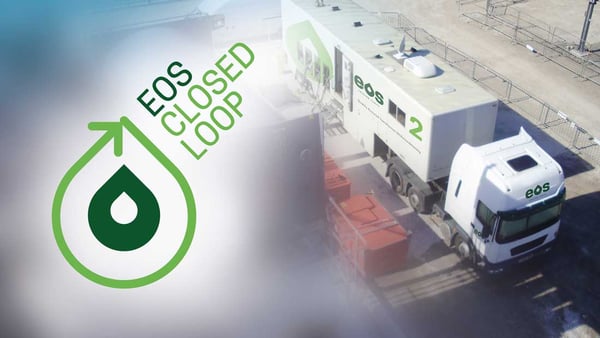
Learn more about our sustainable oil recycling model in this blog:
→ Electrical Oil Services Presents: The EOS® Closed Loop Model
→ EOS® Closed Loop - Be part of the modern circular economy
EOS® BEST PRACTICE
Find out more about our work on these pages:
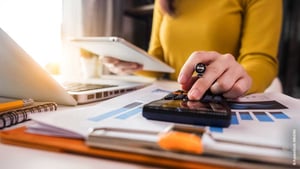
Steel production
Almost like NEW - investing in 20 neglected transformers
Objective: Ensure reliable production by extending transformer lifetime
Solution: EOS® insulating oil regeneration
Step-by-step deep cleaning for twenty 66 kV transformers
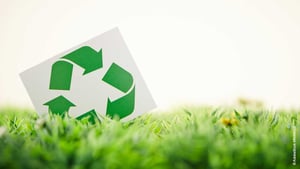
Combined heat and power (CHP) plant
Remove potentially corrosive sulphur from 230,000 litres of transformer oil
Objective: To remove the additive from the 1990s called DBDS
Solution: EOS® insulating oil regeneration
A total of 50 days of thorough deep cleaning to reduce the DBDS content from 100 ppm to <5ppm
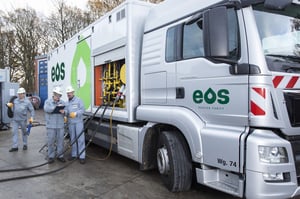
Energy supplier
Extend the service life of transformers by 15 years without high investments
Objective: To deep-clean the insulating oil systems and to remove acids and sludge
Solution: EOS® develops refurbishment strategy for insulating oil regeneration during operation
Start of an era: Making sustainable asset management for transformers possible
.jpg?width=300&name=Electrical_Oil_Services-EOS_4N9A4303_1100x620px_230907_retuschiert%20(1).jpg)
Grid operator
Filling a 132 kV transformer after maintenance work
Objective: Remove contamination and achieve maximum dryness of the insulating oil
Solution: EOS® insulating oil processing
Restore safety with the Mobile Processing Unit (MPU) after warning message
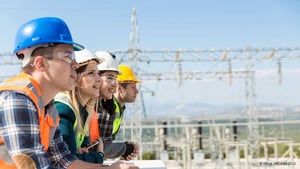
Distribution system operator
Finding a solution when the newly ordered transformer is delivered late
Objective: Put the decommissioned transformer back into operation
Solution: EOS® insulating oil treatment
Drying the oil in the old transformer with extensive vacuum/heat treatment
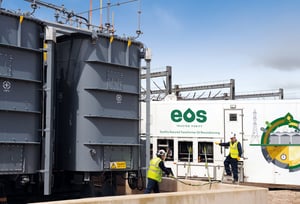
Transformer OEM
Although stored in a dry atmosphere for a long time, the new transformer need to be installed in gas and steam turbine (CCGT) power plants
Objective: To generate a vacuum of less than 1 mbar at low cost and then fill the transformer with insulating oil
Solution: EOS® Mobile Vacuum Unit (MVU) and Mobile Processing Unit (MPU)
Enable cost-effective transformer installation
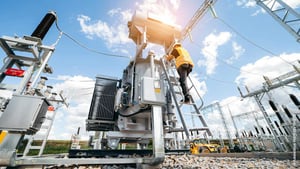
Steel production
Which transformer first? Prepare a professional transformer management system
Objective: Organise monitoring for each individual transformer at the production site to avoid failures
Solution: EOS® develops customised test procedure for regular sampling
Classify transformers according to importance for scheduled transformer oil analyses
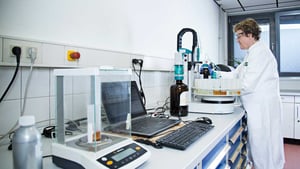
Large power plant
Replace a 275 kV generator transformer and store the insulating oil temporarily
Objective: To store the company's own transformer oil for later re-filling into the new transformer
Solution: EOS® combines Mobile Processing Unit (MPU) and laboratory services with tanker lorries and storage tanks
Oil transport and storage off-site including consistent oil quality monitoring
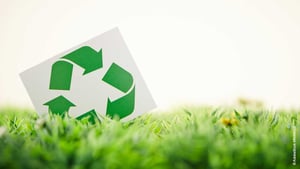
Aluminium company
Sustainably remove 150,000 litres of insulating oil from decommissioned factory
Objective: Remove the insulating oil from the transformers and save the oil
Solution: EOS® organises and monitors the draining of the insulating oil in order to recycle it
Recycling of transformer oil: Collecting the used oil, improve the quality and return the oil to the market as recycled insulating oil
.jpg?width=300&name=Electrical_Oil_Services-EOS_4N9A4303_1100x620px_230907_retuschiert%20(1).jpg)
Distribution grid operator
25,000 litres of insulating oil from the main tank of a 132 kV transformer temporarily stored on site
Objective: To repair tap changers in an ecologically sensitive area and put them back into operation quickly after filling
Solution: EOS® insulating oil processing after interim storage of the transformer oil in an oil-rinsed, certified tanker truck
Insulating oil storage and 2-fold circulation directly and promptly on site
EOS® BEST PRACTICE
Find out more about our work on these pages:
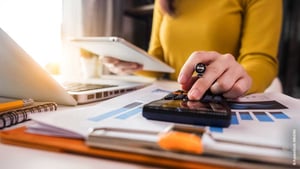
Steel production
Almost like NEW - investing in 20 neglected transformers
Objective: Ensure reliable production by extending transformer lifetime
Solution: EOS® insulating oil regeneration
Step-by-step deep cleaning for twenty 66 kV transformers
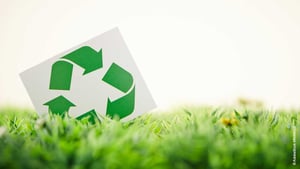
Combined heat and power (CHP) plant
Remove potentially corrosive sulphur from 230,000 litres of transformer oil
Objective: To remove the additive from the 1990s called DBDS
Solution: EOS® insulating oil regeneration
A total of 50 days of thorough deep cleaning to reduce the DBDS content from 100 ppm to <5ppm
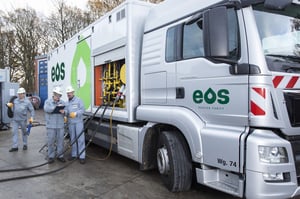
Energy supplier
Extend the service life of transformers by 15 years without high investments
Objective: To deep-clean the insulating oil systems and to remove acids and sludge
Solution: EOS® develops refurbishment strategy for insulating oil regeneration during operation
Start of an era: Making sustainable asset management for transformers possible
.jpg?width=300&name=Electrical_Oil_Services-EOS_4N9A4303_1100x620px_230907_retuschiert%20(1).jpg)
Grid operator
Filling a 132 kV transformer after maintenance work
Objective: Remove contamination and achieve maximum dryness of the insulating oil
Solution: EOS® insulating oil processing
Restore safety with the Mobile Processing Unit (MPU) after warning message
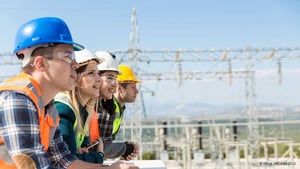
Distribution system operator
Finding a solution when the newly ordered transformer is delivered late
Objective: Put the decommissioned transformer back into operation
Solution: EOS® insulating oil treatment
Drying the oil in the old transformer with extensive vacuum/heat treatment
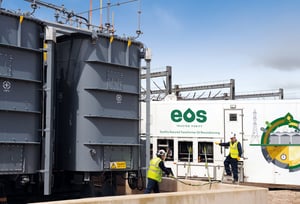
Transformer OEM
Although stored in a dry atmosphere for a long time, the new transformer need to be installed in gas and steam turbine (CCGT) power plants
Objective: To generate a vacuum of less than 1 mbar at low cost and then fill the transformer with insulating oil
Solution: EOS® Mobile Vacuum Unit (MVU) and Mobile Processing Unit (MPU)
Enable cost-effective transformer installation
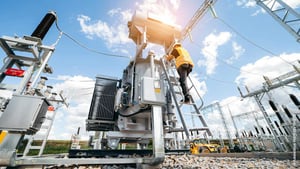
Steel production
Which transformer first? Prepare a professional transformer management system
Objective: Organise monitoring for each individual transformer at the production site to avoid failures
Solution: EOS® develops customised test procedure for regular sampling
Classify transformers according to importance for scheduled transformer oil analyses
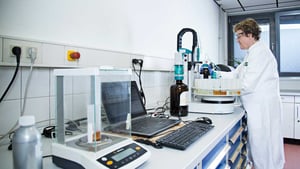
Large power plant
Replace a 275 kV generator transformer and store the insulating oil temporarily
Objective: To store the company's own transformer oil for later re-filling into the new transformer
Solution: EOS® combines Mobile Processing Unit (MPU) and laboratory services with tanker lorries and storage tanks
Oil transport and storage off-site including consistent oil quality monitoring
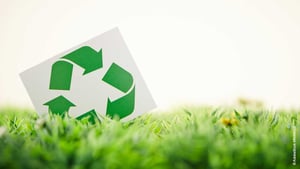
Aluminium company
Sustainably remove 150,000 litres of insulating oil from decommissioned factory
Objective: Remove the insulating oil from the transformers and save the oil
Solution: EOS® organises and monitors the draining of the insulating oil in order to recycle it
Recycling of transformer oil: Collecting the used oil, improve the quality and return the oil to the market as recycled insulating oil
.jpg?width=300&name=Electrical_Oil_Services-EOS_4N9A4303_1100x620px_230907_retuschiert%20(1).jpg)
Distribution grid operator
25,000 litres of insulating oil from the main tank of a 132 kV transformer temporarily stored on site
Objective: To repair tap changers in an ecologically sensitive area and put them back into operation quickly after filling
Solution: EOS® insulating oil processing after interim storage of the transformer oil in an oil-rinsed, certified tanker truck
Insulating oil storage and 2-fold circulation directly and promptly on site